



Tise a
Hatty mwen Hattersley tise. Okòmansman te pote nan zile a kòm yon mak nouvo devinèt flatpacked nan (apeprè) 1940 li te travay pa twa jenerasyon pou prèske 80 ane. Fèt nan fè jete ak bwa li te vin tounen yon travay atistik poukont li. Divots yo sou bra yo kòm li te etabli nan pozisyon, mete nan ba a soti nan ane nan tise men yo, penti yo ta vle chanje koulè ak depo lwil oliv. Tout ede fè chak tise Hattersley inik epi ba yo pwòp pèsonalite yo
Koule a
Koule tissage tradisyonèl yo, tankou sa a mwen te aprann tise nan, yo te blòk oswa estrikti wòch ki pa gen okenn 'konfò' reyèl tankou izolasyon, ekleraj desan, chofaj elatriye Mwen deside mwen te vle yon koule 'chik' e konsa yo te kreye Shed Tissage a. Ki fèt an de mwatye; youn gen egzakteman kantite plas pou Hatty, pirn winder, ankadreman an deformation ak kanpe nan bobin ak lòt la kòm yon boutik estidyo. Koule 'chik' a gen opinyon sansasyonèl sou Loch la, ak anpil espas ak limyè pou wè tise a ak tout pwosesis resi yo.


Tise a
Hatty mwen Hattersley tise. Okòmansman te pote nan zile a kòm yon mak nouvo devinèt flatpacked nan (apeprè) 1940 li te travay pa twa jenerasyon pou prèske 80 ane. Fèt nan fè jete ak bwa li te vin tounen yon travay atistik poukont li. Divots yo sou bra yo kòm li te etabli nan pozisyon, mete nan ba a soti nan ane nan tise men yo, penti yo ta vle chanje koulè ak depo lwil oliv. Tout ede fè chak tise Hattersley inik epi ba yo pwòp pèsonalite yo
Weaver la
Non mwen se Miriam Hamilton epi mwen te aprann tise nan otòn 2018, ansyen pwopriyetè Hatty, yon mesye k ap fè 90 an, te anseye. ti tise yon ti koule frèt kote li te trese pandan 50 ane. Li te eritye tise a nan men papa l ', ki te achte l' orijinal nan faktori Hattersley nan Keighley, Yorkshire.
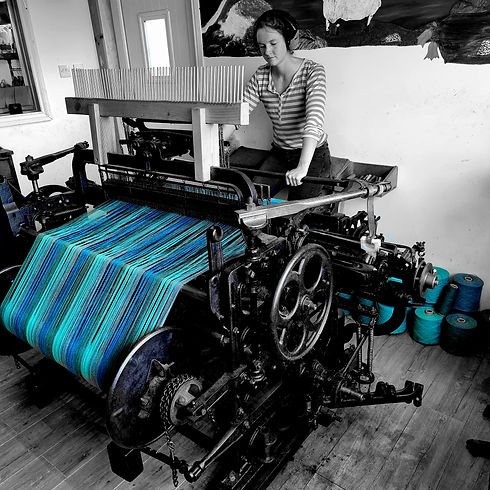
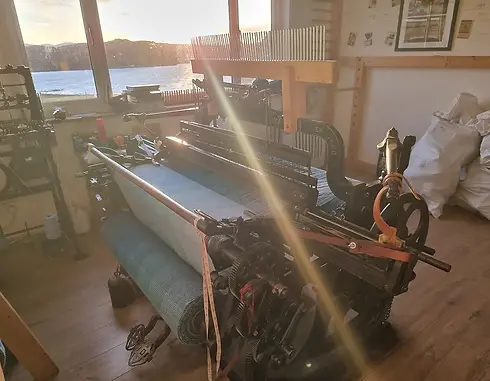
Koule a
Koule tissage tradisyonèl yo, tankou sa a mwen te aprann tise nan, yo te blòk oswa estrikti wòch ki pa gen okenn 'konfò' reyèl tankou izolasyon, ekleraj desan, chofaj elatriye Mwen deside mwen te vle yon koule 'chik' e konsa yo te kreye Shed Tissage a. Ki fèt an de mwatye; youn gen egzakteman kantite plas pou Hatty, pirn winder, ankadreman an deformation ak kanpe nan bobin ak lòt la kòm yon boutik estidyo. Koule 'chik' a gen opinyon sansasyonèl sou Loch la, ak anpil espas ak limyè pou wè tise a ak tout pwosesis resi yo.
A wee video showing some of the processes involved in creating the a tweed! If you don't like the music, mute it then unmute at the weaving part to hear the sound of the loom.
To actually make a tweed from start to finish takes several months from raw fleeces to finished cloth.
Once the sheep have been sheared and the fleeces picked clean of vegetable matter and poop, they are sent to the mill for spinning. First the raw wool is put into a machine that gently submerges and withdraws it from the water gradually moving down the belt as the water gets dirty meaning it uses less water overall. The fleeces are then dried and, once completely dry, picked and separated before being fed into the carding machine. Here it gets drawn through lots of rollers which brush the fibers into alignment. It comes out as a soft fluffy rolag and is stored in large drums. The rolags are fed into another machine that spins them into yarn.
Once back with us we need to turn the yarn into cloth.
First we have to make the warp. Between 6 and 24 cones of yarn fit on our bobbin stand, the threads are drawn off and wrapped around the warping frame on the wall. Each series of wraps gives the total finished length of the tweed. We normally weave around 60 meters, for the gotland it was 20. So depending on the number of threads used its anything between 29 to 116 wraps.
Once all wrapped the warp is chained up to keep it tidy, then beamed onto the loom.
The final step is tying 696 knots to join the old and the new warp together so the warp can be pulled through the heddles onto the loom ready to weave!
Before we can start weaving we have to wind the pirns using the other machine we have in the corner. These go inside the shuttles and cary the weft through the warp to make the cloth.
When each peddle is depressed that turns the lower shaft. That turns the teardrop shape cams which causes the picker arms to fling inwards, driving the shuttle. The lower shaft has a cog afixed to it which turns a larger cog attached to a block of cams. These control the heddles (the metal reeds in wooden frames) causing them to be raised or lowered in a set order. This raises or lowers the warp threads in a set order to create the 'shed' the shuttle flies through. That is the gap in the warp created by the heddles lifting different threads up in turn. This creates the over/under/over/under weave of tweed. We can change the order of the threads to get different weaves e.g. herringbone, twill, honeycomb, basketweave etc.
The lower shaft also turns the arm which controls the complex series of cogs on the righthand side of the loom that pull the fabric through the loom at exactly the right speed as it is woven. On each side of the loom are two large wheels, these turn the top wheels which turns the top shaft. That pushes the beater in and out every shot (press of a peddle) to beat the cloth to the correct tension. On the left hand side of the loom is a very complicated series of rods and cams that should control which way the shuttle box turns and how frequently. We have disabled ours however to put less stress on the loom after our lower shaft snapped twice!
Once the weaving is finished it gets pulled off the loom, folded into a bale and gets sent to a mill in Galashiels where it goes through a number of finishing processes. First it is washed, drawn through giant rollers that beat the cloth causing it to shrink (full) and bind the individual yarns together. This gives the cloth its strength and durability. Then it is stretched to its finished width and drawn flat through a drier to set the tweed. Then it is drawn through another machine with fine blades that crop the surface leaving it smooth and fluff free. Finally it is pressed and measured and sent back here!
Two Sisters Tweeds
You can now browse the website to buy either ready made products or fabric sold from the quarter meter
so you can order as much or as little as you want!
Weaving to Order
-
-
We are always happy to discuss weaving commissions. We can weave with your own yarn spun from your sheep's fleeces or we can design a tweed together based on yarn from our suppliers. We require a minimum order of 30 meters and can weave these main pattern styles; a block check, patchwork, multicolour warp, over check or a combination of the above. We can't weave tartan/plaid, houndstooth or complex checks due to the age and limitations of our 85 year old looms. For an idea of styles available please see our tweed range or previous works.
-
-
Tweeds are £40 per meter if you supply yarn and from £50 per meter if we supply the yarn depending on the cost of the yarn chosen. This price would be for supersoft lambswool or Shetland. We can also offer merino, heritage natural undyed and more!
-
-
If you are going to have yarn spun for us to weave with please confirm with us first the quantities, yarn weight and colours as otherwise we may not be able to weave exactly what you had in mind!
-
-
We are also happy to discuss making your bespoke tweed into products either for you to sell on or for yourself. These are costed on an individual basis based on the items and quantities required. Bare in mind that we are a very small team of three sisters and cannot do large bulk orders!
-
-
Please note we do not, and cannot weave Harris Tweed due to the mill being unwilling to reliably supply yarn or finish (wash) our tweeds
-
-
Here are examples of commissions we have done in the past;
Here the customer wanted an overcoat and matching waistcoat made in his own unique tweed. We did actually weave less than 30 meters in this instance as we wove the rest of the warp in a different colour for our own use. The customer chose the three warp colours and the fantastic contrasting orange weft, then designed the coat and waistcoat with me and I made it to his specifications.
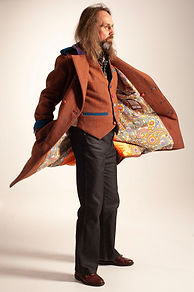
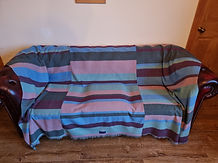



This collection of blankets was ordered as gifts for the couples children, woven in their school colours. This is merino yarn so beautifully soft for snuggling under! I even hand embroidered their initials on them
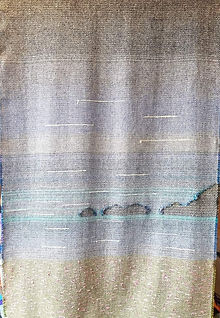
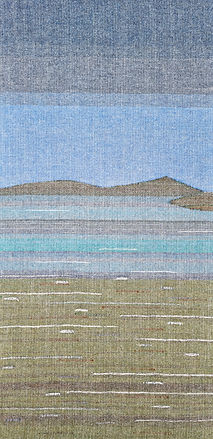
We can even weave wall hangings to order to look like a landscape special to you. We can create (to an extent) mountains and rocks etc. add different colour "flowers" and generally personalise. These are the most difficult to acheive as they are abstract and not an exact rendering of the photo. Where the shaped sections are will often be wee gaps but since it is a wall hanging these all become part of the charm of being woven on such an old loom!
This beautiful blue-faced Leicester yarn belonging to the customer was spun and dyed by our usual mill The Border Mill. We had a slight hiccup as the customer hadn't asked us what quantities were needed for the pattern they originally wanted before ordering the yarn so we had to modify the design based on the available colours and quantities. But it turned out absolutely stunning - I'd have happily kept it!




My biggest commision to date - this was for the Scottish Travel Society, two 60 meter rolls of tweed in their own unique design. I sold the products on my own website and made them to order for their members. Over 200 scarves plus shawls, throws and more!
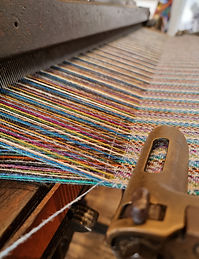
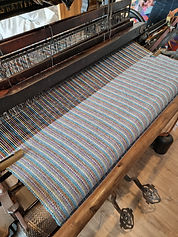

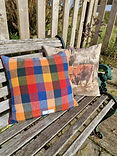
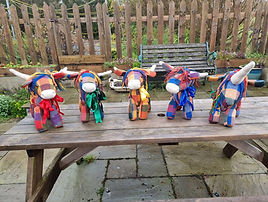
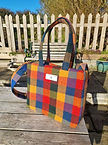

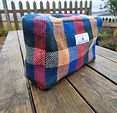
This commission was a big one! 30 meters of tweed woven in a block check in the customers colours, which I then turned into blankets, cushions, scarves, bags, heilan coos and a unicorn!


Woven in the customers own Hebridean yarn with accents of Shetland this tweed I turned into a collection of throws for the customer to sell in their shop

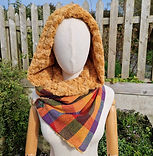

This customer has ordered two years in a row! This sublime yarn is from Icelandic Leader Sheep and is incredible to work with. It was very finely spun so created a lovely lightweight warm cloth. We wove four rolls in the various colourways to showcase the different sheep colours.
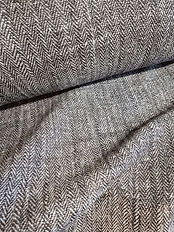.jpeg)
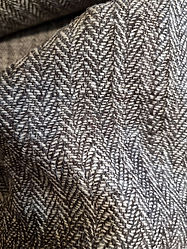.jpeg)
